Anticorrosion application of rotary kiln
Rotary kiln is the most important equipment in cement production line, and its stable operation is directly related to the output and quality of cement clinker. However, in recent years, there have been frequent problems with the rotary kiln shell, such as deformation, cracks, and even fractures, resulting in considerable direct and indirect losses, and even safety problems. There are many reasons for these problems, such as service time, weather, operator's operation, etc. One of the most important factors is the corrosion of the rotary kiln cylinder, which will make the cylinder thinner and reduce the bearing capacity, resulting in the above-mentioned problems.
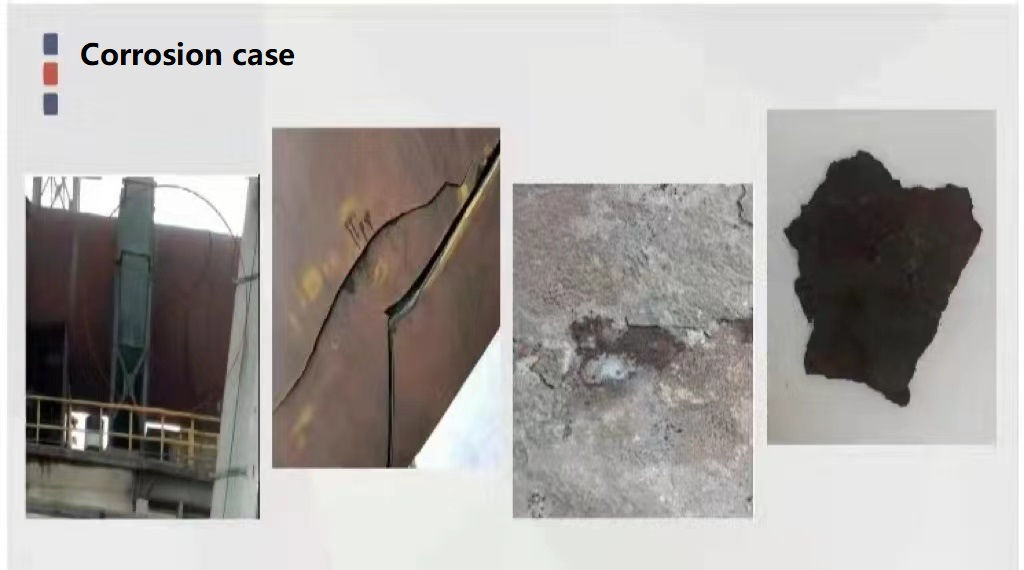
In addition to the high temperature, certain corrosive gases will also be generated in the process of calcination clinker in the rotary kiln, especially in the production line of co-processing waste, a large amount of harmful gases such as sulfur oxides, nitrogen oxides, hydroxides, chlorine, etc. will be generated. These gases react chemically with water to form very corrosive acid-base substances, which will seriously corrode the inner wall of the rotary kiln. According to the engineer of a cement plant, the inner wall of the company's rotary kiln corroded by 1 mm in just half a year. If no anti-corrosion measures are taken, even a brand-new rotary kiln will be prone to problems after more than ten years of use.
The anti-corrosion of the inner wall of the rotary kiln can use SY-high temperature wear-resistant anti-corrosion coating. The characteristics of this product are as follows:
1. The coating is dense, high hardness, wear-resistant and impact-resistant, and resistant to erosion by smoke and dust particles;
2. The coating is resistant to high temperature medium corrosion such as sulfide, nitrogen oxide, HCl gas and salt spray, resistant to "dew point" corrosion of condensate water, and resistant to alternating acid and alkali corrosion in the process of desulfurization and denitrification;
3. The coating has a long service life and good durability, and the damaged coating is easy to repair;
4. High coefficient of linear expansion, good adhesion, and strong bonding force with the substrate;
5. High thermal shock resistance, flue gas temperature is alternating high and low, the coating does not fall off, and there is no crack;
6. The surface of the coating film is smooth, with a certain self-cleaning effect and anti-tar adhesion.
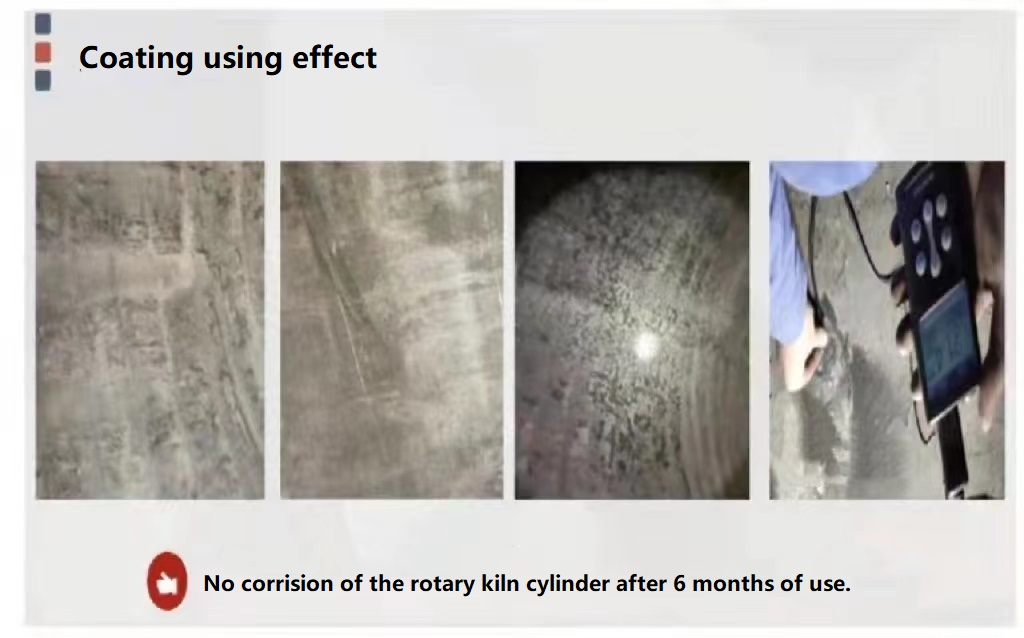
It can be seen from the product features that SY-high temperature wear-resistant and anti-corrosion coating is not only resistant to acid, alkali and high temperature, but also has good adhesion, which is equivalent to putting a layer of protective clothing on the inner wall of the rotary kiln, which can strongly resist chemical and physical damage, so as to protect the rotary kiln from the corrosion damage of acid and alkali high temperature.
Post time: Mar-31-2022